I. Excellent Characteristics and Applications of HDPE Pipe
In the modern engineering field, HDPE (High-Density Polyethylene) pipe have become the preferred material for numerous pipeline systems due to their outstanding performance and wide applicability. HDPE pipe exhibit excellent characteristics such as chemical corrosion resistance, low friction coefficient, high toughness, and exceptional sealing performance. These properties make them widely applicable in areas such as water supply, drainage, gas transmission, and chemical fluid transport.
II. Factors to Consider in Designing HDPE Pipe Systems
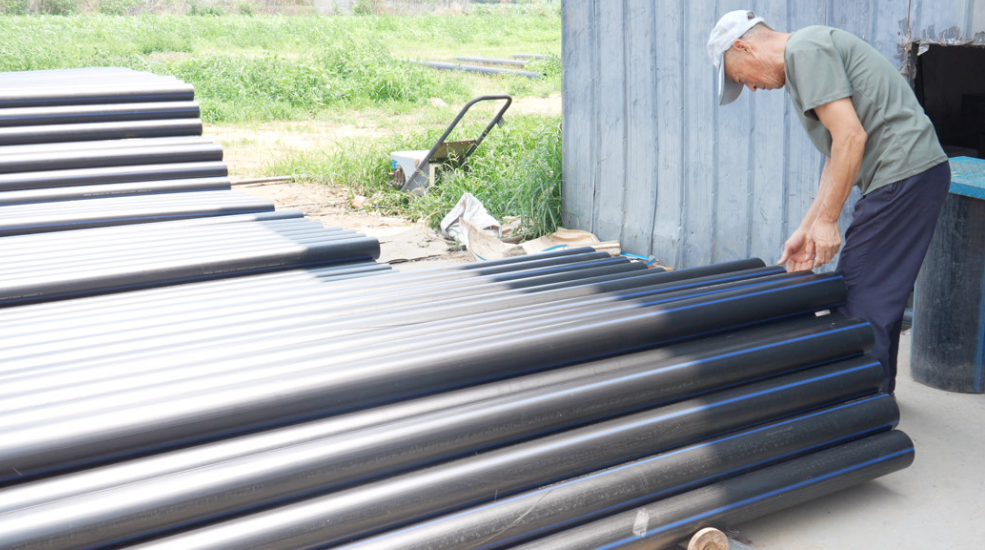
- Clear Understanding of System Usage and Operating Conditions
When designing HDPE pipe systems, it is essential to first understand the system's purpose and operating conditions. This includes the nature of the transported fluid (such as temperature, pressure, chemical composition, etc.), flow rate requirements, and potential external environmental impacts (such as soil type, geological conditions, climate factors, etc.). For water supply pipe systems, water quality hygiene requirements are crucial, while drainage pipes require consideration of sewage composition and discharge volume. - Selection of Pipe Sizes and Specifications
Choosing the right pipe sizes and specifications is a critical aspect of the design process. Based on flow calculations and flow velocity requirements, along with standard specifications for HDPE pipe, select the appropriate diameter. An undersized diameter can lead to excessively high fluid flow velocities, increasing pressure loss and pipe wear, while an oversized diameter can raise costs and installation difficulty. - Design of Pipe Layout and Alignment
The design of pipe layout and alignment needs to consider construction convenience, maintenance feasibility, and overall system layout. It is important to minimize the number of bends and fittings to reduce resistance and potential leakage risks. When crossing areas with significant terrain variations, it is necessary to strategically place inspection chambers and air release valves to ensure the system operates smoothly. - Selection of Connection Methods and Pipe Support
HDPE pipe offer various connection methods, including heat fusion, electrofusion, and mechanical connections. During the design phase, choose an appropriate connection method based on specific engineering conditions and construction requirements, ensuring the quality and reliability of connections. Additionally, consider pipeline support and fixation to prevent displacement and vibrations during operation. - Pressure Analysis and Strength Calculations
Pressure analysis and strength calculations are essential during the design process. Based on the fluid pressure and pipe operating temperature, determine the wall thickness and material grade to ensure the pipe can withstand internal pressure and external loads. For buried pipe, consider soil backfill and compaction requirements, as well as the impact of surface traffic loads on the pipe. - Corrosion Prevention and Protective Measures
Corrosion prevention and protective measures are crucial aspects of the design process. Implement appropriate corrosion coatings or cathodic protection measures based on the usage environment to extend the pipe's lifespan. For pipelines exposed to sunlight, UV protection should also be considered.
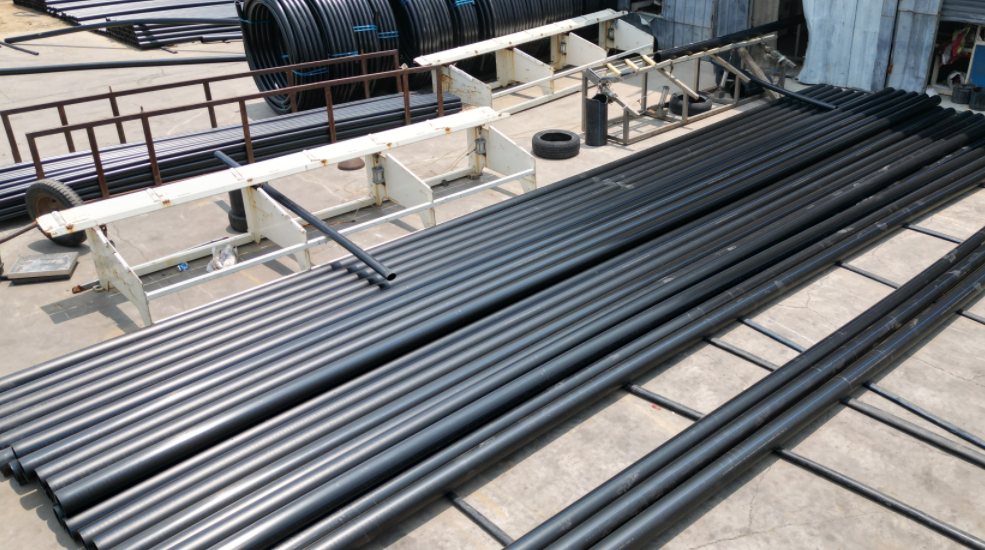
III. Installation Considerations for HDPE Pipe Systems
During the installation of HDPE pipe systems, several considerations must be taken into account. Construction personnel should undergo professional training to be familiar with the installation process and technical requirements of HDPE pipes. Prior to installation, carefully inspect pipelines and fittings to ensure they are free from damage, deformation, and impurities. Use specialized tools for cutting pipes to ensure smooth and perpendicular cuts.
- Key Points for Heat Fusion and Electrofusion Connections
During heat fusion connections, control heating temperature, time, and pressure to ensure a secure, leak-free connection. For electrofusion connections, follow equipment operation procedures to ensure correct welding parameters. - Proper Operation of Mechanical Connections
Ensure that components of mechanical connections are correctly installed, and that sealing elements are intact. - Considerations for Pipe Installation
During pipe laying, avoid excessive stretching or bending of the pipeline to prevent damage. For buried pipes, follow design requirements for layer-by-layer backfilling and compaction to prevent voids and uneven settling. - Pressure Testing and Leak Inspection After Installation
After installation, conduct rigorous pressure testing and leak inspections to verify the reliability of the pipe system.
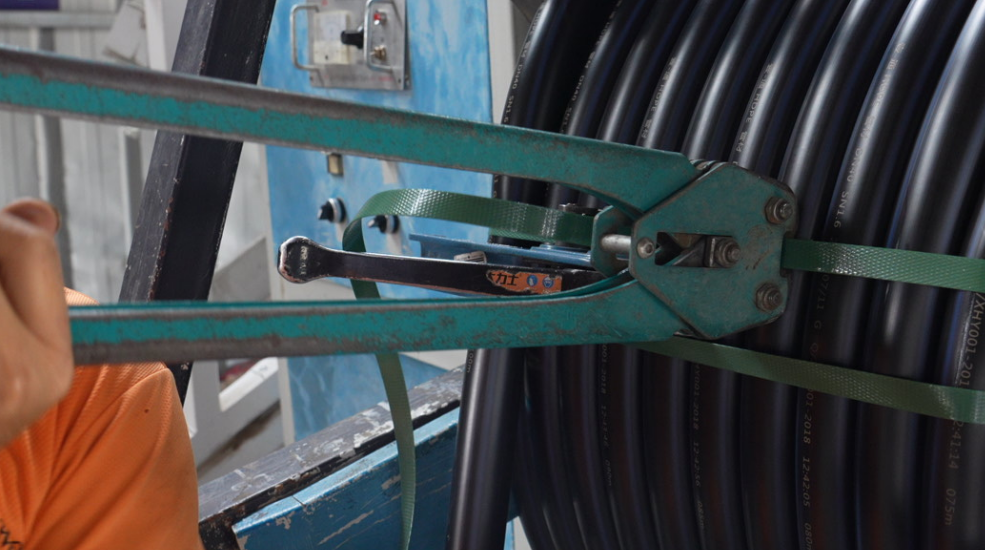
Only through scientifically sound design and standardized installation can the advantages of HDPE pipes be fully realized, providing high-quality and reliable pipeline transport solutions for various engineering projects.
You are welcome to : phone call, Message, Wechat, Email& Seaching us, etc.