What are HDPE Electrofusion and Butt Fusion Fittings?
- Electrofusion Fittings
HDPE E/F fittings are specially designed to connect HDPE pipes through an electrofusion welding process, ensuring a strong and sealed connection. These fittings contain embedded resistance wires that generate heat when an electric current passes through them. This heat melts the inner surface of the fitting and the outer surface of the inserted HDPE pipe, fusing them together to create a robust connection. - Butt Fusion Fittings
HDPE butt fusion fittings are used to connect HDPE pipes through a butt fusion welding process. This method involves heating the ends of the pipe and the fitting until they melt, then pressing them together under pressure to form a solid, seamless connection once cooled.
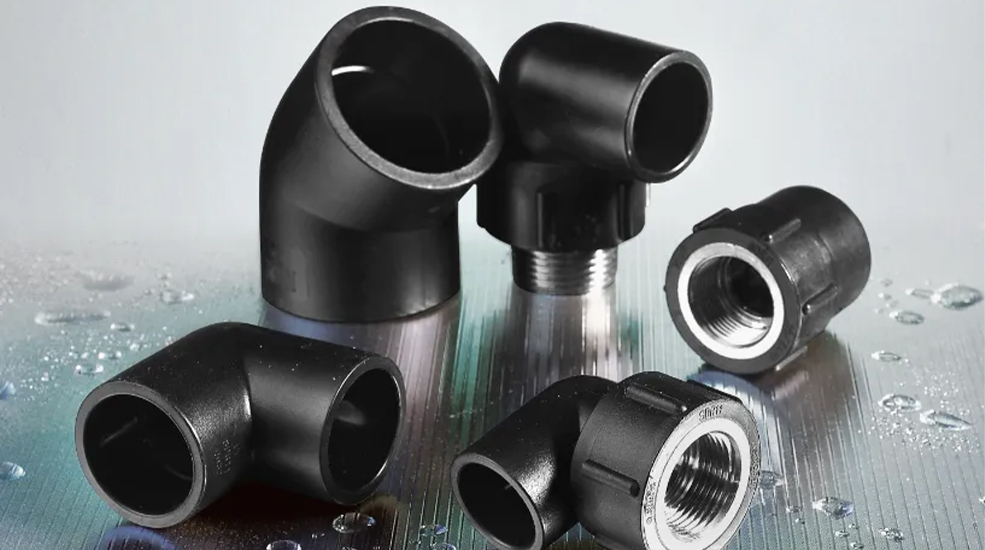
Characteristics of HDPE Electrofusion Fittings
- Strong Connection
After welding, the E/F fittings form a homogeneous connection with the HDPE pipe, resulting in a joint stronger than the pipe itself, ensuring no leakage due to external forces or internal pressure. - Chemical Resistance
Since the entire fitting is made from HDPE material, it has excellent chemical resistance, making it suitable for transporting chemicals, gases, or wastewater. - High Automation
The electrofusion welding process is typically automated, with the welding machine controlling the time and temperature according to preset programs, ensuring consistent welding quality. - Fast Installation
The electrofusion welding process is straightforward and doesn’t require complex equipment, making it efficient and particularly suitable for on-site installations. - Wide Range of Applications
HDPE pipe fittings are suitable for connecting various HDPE pipes, commonly used in gas pipelines, water supply pipelines, sewage pipelines, and chemical pipelines. - Various Types
HDPE E/F fittings come in different types, such as elbows, tees, end caps, and couplers, catering to various connection needs. - High Pressure Resistance
The piping system connected through electrofusion exhibits excellent pressure resistance, capable of withstanding high working pressures. - Environmental Stress Crack Resistance
HDPE material has good resistance to environmental stress cracking, ensuring long-lasting durability and stability of the piping system.
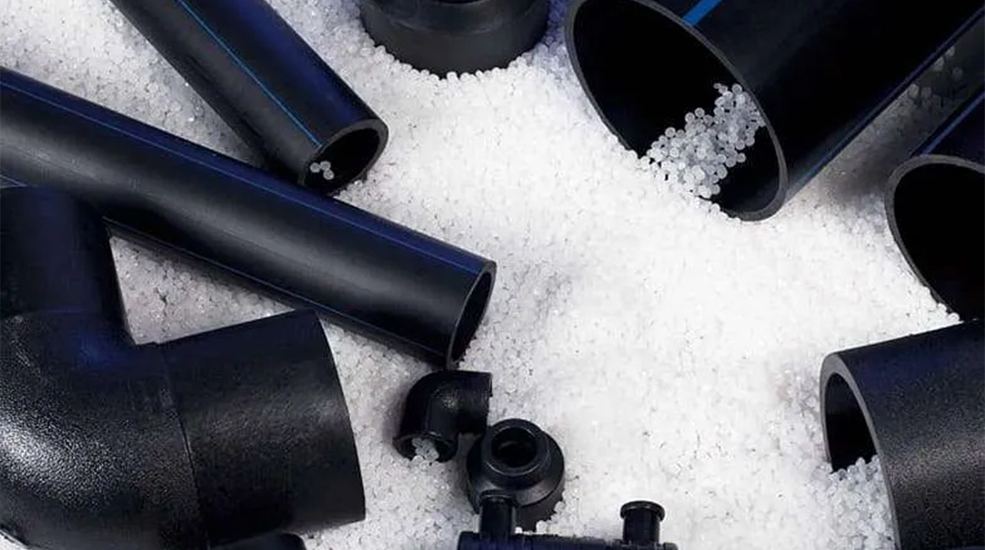
Characteristics of HDPE Butt Fusion Fittings
- High-Strength Connection
HDPE butt fusion fittings, when welded, form a monolithic connection with the pipe, typically stronger than the pipe itself. This ensures the entire piping system is highly durable and leak-proof, especially suitable for applications requiring high sealing standards. - Corrosion Resistance
The HDPE material itself is highly resistant to chemical corrosion, making butt fusion fittings ideal for handling corrosive media, such as pipelines transporting acidic, alkaline, or saline solutions. - Temperature Resistance
HDPE butt fusion fittings can maintain their physical properties across a wide temperature range, making them suitable for pipeline applications in both cold and hot environments. They won’t experience significant dimensional changes or performance degradation within the working temperature range. - Easy Installation
Butt fusion welding equipment is relatively simple to operate, and the welding process is easy to master, making it suitable for on-site installation, especially in remote locations. The welding process doesn’t require additional materials or fittings, simplifying the installation process. - Wide Applications
HDPE butt fusion fittings are available in various types, including couplers, elbows, and tees, making them suitable for a wide range of pipeline connection needs. They are widely used in municipal engineering (such as water supply and drainage), gas transmission, industrial pipelines, and agricultural irrigation.
Differences Between the Two
HDPE electrofusion and butt fusion fittings are both used to connect HDPE pipes, but they differ significantly in terms of connection method, construction process, application scenarios, and equipment requirements. The following are the detailed differences:
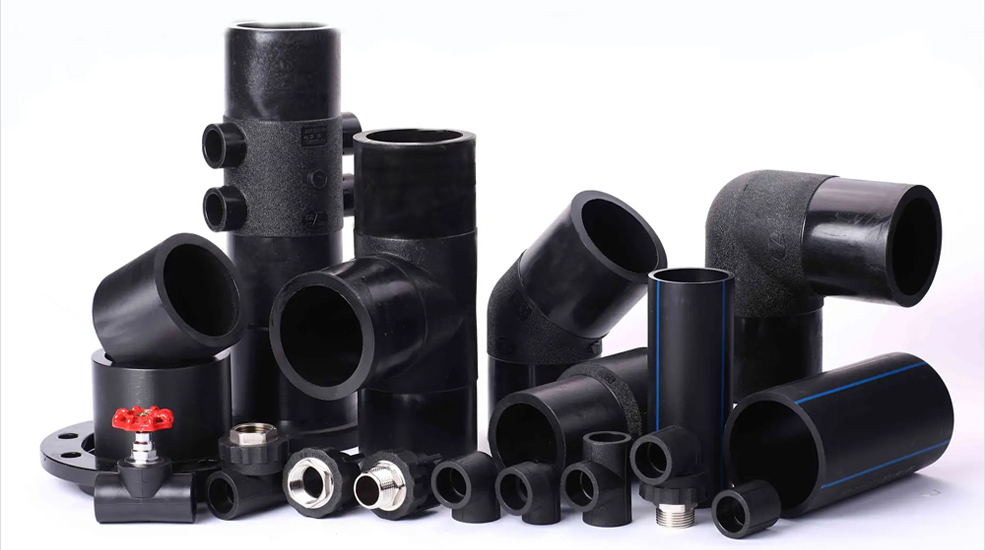
Connection Method
- Electrofusion Fittings
Utilize embedded resistance wires within the fitting. When an electric current passes through, these wires heat up, melting the inner surface of the fitting and the outer surface of the inserted HDPE pipe, fusing them together. Only the inner surface needs to be heated during welding, with no need to heat the entire end face. - Butt Fusion Fittings
The ends of the pipe and the fitting are directly heated using a heating plate until they reach a molten state. They are then pressed together under pressure, forming a strong connection once cooled. The entire end face must be heated during welding.
Construction Process
- Electrofusion Fittings
Highly automated, with the welding machine typically controlling the time and temperature. It is easy to operate and suitable for on-site construction. It has lower alignment requirements for the pipe, making it ideal for complex or hard-to-align connections, such as repairs or installations in tight spaces. Better suited for small-diameter pipes and complex fitting structures. - Butt Fusion Fittings
Requires a higher skill level from operators, needing precise control over welding temperature and pressure. It requires accurate alignment of the pipe and fitting axes to ensure quality welding, making it suitable for straight pipe runs and regular piping systems. Usually used for large-diameter pipes, where achieving high-quality connections through electrofusion would be challenging.
Equipment Requirements
- Electrofusion Fittings
Requires a specialized electrofusion welding machine, which controls the welding process through electrical current. These machines are typically small and portable, with low power consumption, making them suitable for job sites with limited power supply. - Butt Fusion Fittings
Requires the use of a butt fusion welding machine, which is larger and requires heating plates and clamps for heating and aligning the fitting with the pipe. These machines usually have higher power requirements, making them more demanding in terms of site power supply.
Application Scenarios
- Electrofusion Fittings
Commonly used for small-diameter pipes, repair or retrofit projects, and complex pipeline connections like tees and reducers. They are widely used in urban gas transmission pipelines and potable water pipelines due to their high sealing performance and ease of operation. - Butt Fusion Fittings
Typically used for large-diameter main pipelines, such as water supply, sewage treatment, and industrial pipelines. They are well-suited for large-diameter, long-distance pipeline systems, where their high-strength connection can handle high pressure and flow rates.
Cost
- Electrofusion Fittings
Generally have a higher cost in terms of manufacturing and equipment. However, in complex projects, the high reliability and ease of operation can save time and labor costs. - Butt Fusion Fittings
Typically have lower costs for both the fittings and the welding equipment, making them suitable for large-scale, long-distance pipeline connections.
Conclusion
As hdpe pipe fittings,HDPE E/F fittings and butt fusion fittings each have their own advantages and disadvantages, with the choice depending on the specific engineering needs. Electro Fusion fittings are suitable for small-diameter, complex pipeline connections, and scenarios with high sealing requirements, while butt fusion fittings are ideal for large-diameter, long-distance straight pipeline connections. The choice between the two depends on the construction conditions and requirements in actual applications.
You are welcome to : phone call, Message, Wechat, Email& Seaching us, etc.