Electrofusion welding is a highly efficient and reliable method used for connecting high-density polyethylene (HDPE) pipes, which are widely utilized in the construction of water, gas, and sewage systems. This advanced technique is crucial in projects that demand leak-proof joints, durability, and ease of installation. In this article, we will delve into the electrofusion welding process, the equipment required, and its applications in the construction and industrial sectors.
What is Electrofusion Welding?
Electrofusion welding is a technique that joins HDPE pipes using specialized fittings with built-in electrical heating elements. These fittings, known as electrofusion fittings, are designed to fuse the pipe material to create a strong and seamless joint. When connected to an electrofusion welding machine, electrical energy is passed through the embedded heating coils in the fitting, causing the surrounding HDPE material to melt and bond with the pipe.Electrofusion welding is particularly effective for complex pipe networks with numerous joints or where space is limited, as it requires minimal equipment and preparation.
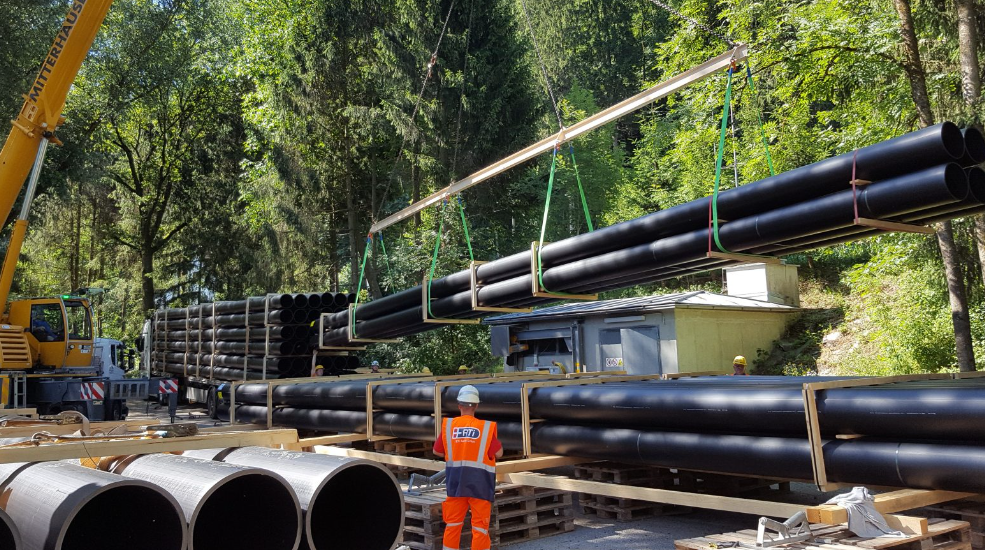
How Electrofusion Welding Works
- Preparation of the Pipes
The pipe ends must be properly cleaned and prepared before the welding process begins. This involves scraping the surface to remove any oxidation or contaminants that might interfere with the fusion. The cleanliness of the pipe and fitting surfaces is essential to ensuring a strong bond. - Positioning the Fitting
The electrofusion fitting is then placed onto the prepared pipe ends. The fitting contains small heating elements that will generate heat when the machine is activated. - Connecting to the Electrofusion Machine
The electrofusion machine is connected to the fitting using its terminals. The machine applies a programmed current to the embedded heating elements, which heats the pipe and fitting material to the correct melting temperature. - Fusion Process
As the HDPE material melts, it bonds with the pipe surface. The welding machine regulates the heat and duration of the weld, ensuring a consistent and reliable joint. This process eliminates the need for external heat sources like flames, which makes it safer, especially in confined spaces. - Cooling
Once the welding is complete, the joint must be allowed to cool down and solidify. Moving or disturbing the pipes during the cooling phase could result in a compromised joint.
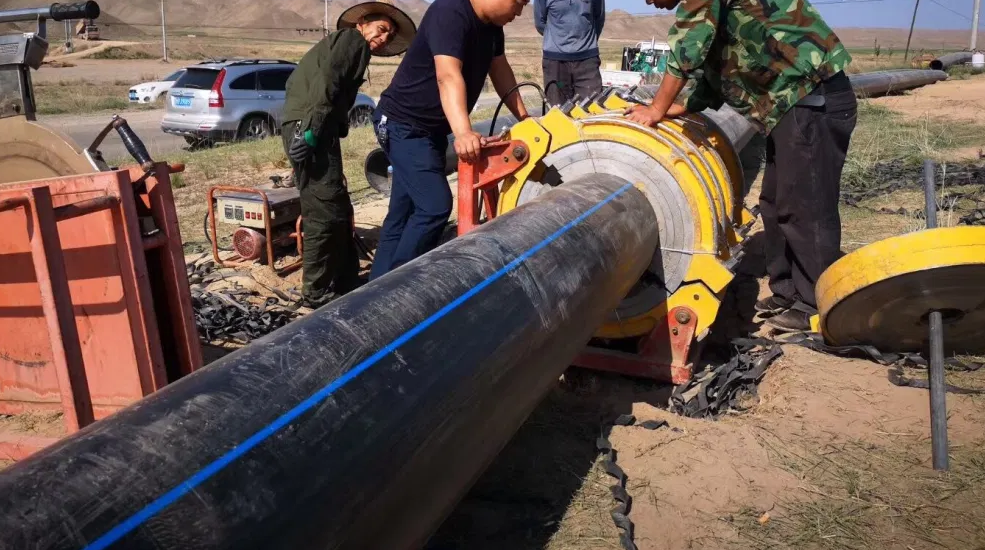
Benefits of Electrofusion Welding
- Precision and Reliability
The electrofusion process ensures precision in every weld, leading to high-strength joints that can withstand internal pressure and external forces. The risk of joint failure is minimized, making this method ideal for critical applications. - No Need for Open Flames
Since the process relies on electrical energy to heat the material, no open flames or external heat sources are required. This is a significant safety advantage, especially in hazardous environments like gas pipelines. - Ideal for Confined Spaces
Electrofusion welding requires minimal equipment, making it possible to perform in tight or confined spaces where other methods might be difficult or impossible to use. This makes it a go-to option for complex or underground installations. - Leak-Proof Joints
Electrofusion welding is known for creating seamless, leak-proof joints, which are critical in water and gas pipelines. The strength of the joints ensures that the system remains safe and operational for extended periods. - Durability and Longevity
HDPE pipes joined using the electrofusion method are highly durable and resistant to environmental stressors such as temperature fluctuations, corrosion, and chemical exposure. This makes the system long-lasting and cost-effective over time.
Electrofusion Welding Machine
The heart of the electrofusion welding process is the electrofusion machine, which provides the electrical energy required to heat the fittings. These machines are designed to regulate the current and temperature precisely, ensuring that the fusion process is carried out accurately.
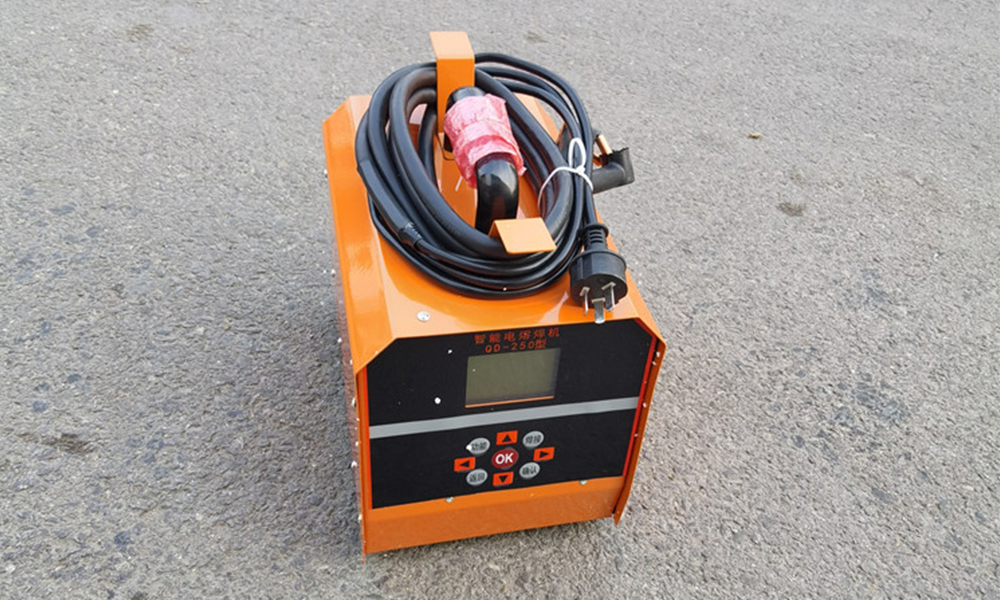
Key features of an electrofusion welding machine include:
- Automated settings
Many modern machines come with pre-programmed settings that are specific to different pipe sizes and materials, making the welding process straightforward and reducing the chances of error. - Portability
Electrofusion machines are often compact and portable, allowing them to be used on various job sites, including remote or difficult-to-access areas.
Applications of Electrofusion Welding
- Water Distribution Systems
In water supply networks, HDPE pipes are used extensively due to their resistance to corrosion and long service life. Electrofusion welding ensures that joints are leak-proof, preventing water loss and contamination. - Gas Pipeline Systems
The precision and reliability of electrofusion welding make it a preferred method for installing gas distribution networks. The risk of leaks is minimized, ensuring safety in the transport of gas. - Sewage and Wastewater Systems
HDPE pipes are also commonly used in sewage and wastewater systems, where chemical resistance and durability are key. Electrofusion welding ensures that the joints can withstand the aggressive environment of these systems. - Mining and Industrial Applications
HDPE pipes are favored in mining and industrial applications due to their ability to withstand harsh chemicals and abrasive materials. Electrofusion welding is often used to join these pipes, ensuring that the systems are reliable and require minimal maintenance.

Considerations in Electrofusion Welding
- Proper Pipe Preparation
The cleanliness of the pipe surface is critical to achieving a good weld. Failure to properly clean and scrape the pipe ends can result in a weak bond, leading to leaks or joint failure. - Skilled Labor
Although electrofusion welding is relatively straightforward, it requires trained technicians to ensure that the process is carried out correctly. Missteps in the welding process can compromise the integrity of the joint. - Cost of Fittings
Electrofusion fittings can be more expensive compared to other joining methods, but the long-term reliability and strength of the joints often outweigh the initial cost.
You are welcome to : phone call, Message, Wechat, Email& Seaching us, etc.