An HDPE (High-Density Polyethylene) pipe welding machine is a specialized tool used to join HDPE pipes and fittings using heat fusion techniques. This process involves heating the ends of the pipes and then applying pressure to fuse them together, creating a strong, durable, and leak-free joint. HDPE pipes are commonly used in applications such as water distribution, gas pipelines, and sewer systems due to their flexibility, corrosion resistance, and long lifespan.
There are two main types of welding methods used for joining HDPE pipes:
1. Butt Fusion Welding Machine:
- Function: This is the most common method for joining HDPE pipes. The butt fusion machine heats the ends of two pipes (or a pipe and a fitting) to a specific temperature and then presses them together with a specified force to form a strong bond.
- Components:
- Clamping System: Holds the pipes in place during the welding process.
- Heater Plate: A flat heating plate that is placed between the pipe ends to melt the material.
- Hydraulic System: Provides the pressure needed to fuse the pipes.
- Control Unit: Regulates temperature, pressure, and time during the process.
- Key Features:
- Works with a wide range of pipe sizes (typically from 32 mm to 1600 mm in diameter).
- Suitable for both PE100 and PE80 materials.
- Produces high-strength, permanent joints.
- Advantages:
- Reliable and long-lasting joints.
- Suitable for a variety of applications.
- No need for additional materials like welding rods.
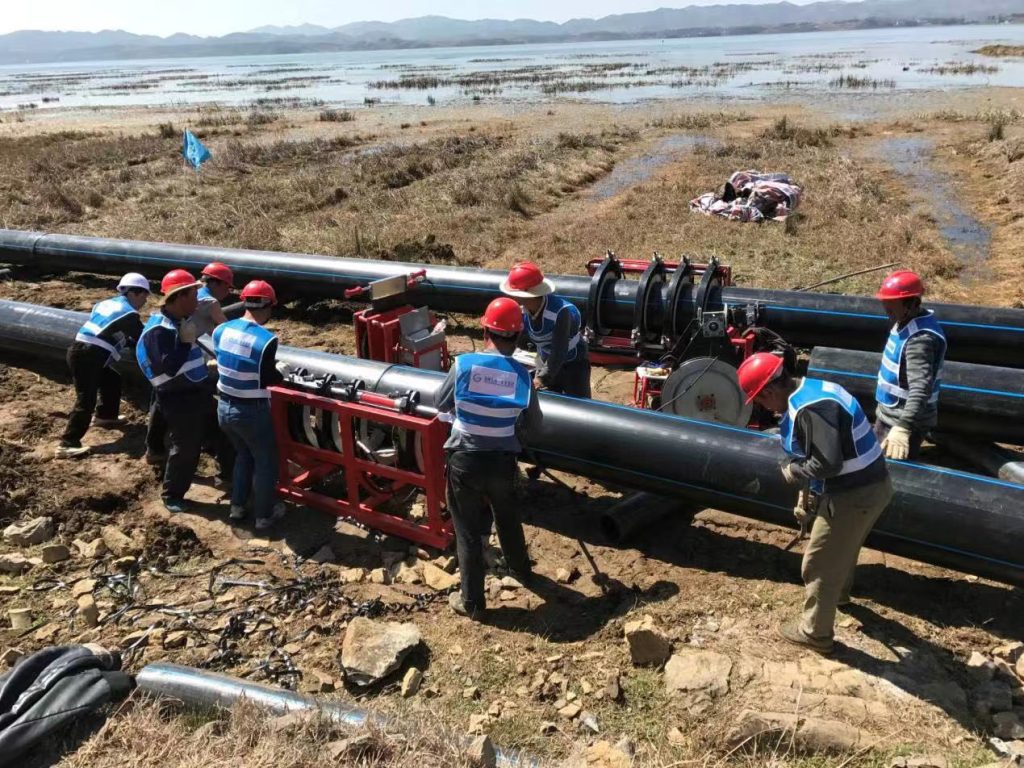
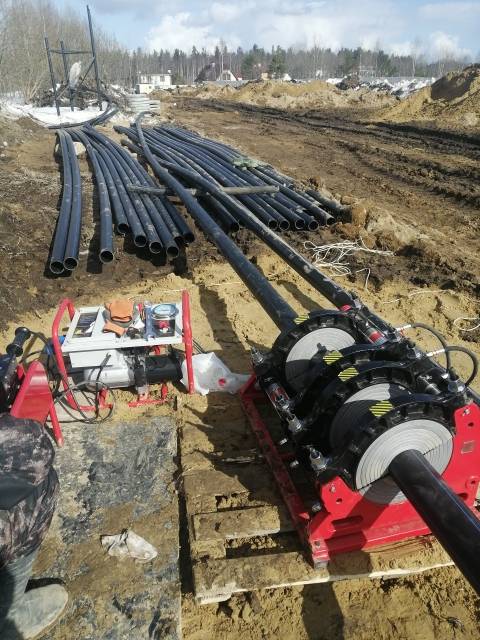
2. Electrofusion Welding Machine:
- Function: Electrofusion involves the use of electrofusion fittings, which have embedded heating elements. The machine applies an electrical current to these elements, generating heat that melts the pipe and fitting to form a bond.
- Components:
- Electrofusion Machine: The machine is used to supply electrical current to the fittings for fusion.
- Electrofusion Fittings: These fittings contain built-in heating coils or elements.
- Key Features:
- Works with smaller pipes (typically up to 315 mm in diameter).
- Often used for repairs or in situations where a butt fusion machine is not practical.
- Faster and easier to operate for smaller jobs.
- Advantages:
- Ideal for repairs, tight spaces, or when butt fusion is not feasible.
- No need for heat plates.
- Suitable for smaller or medium diameter pipes.
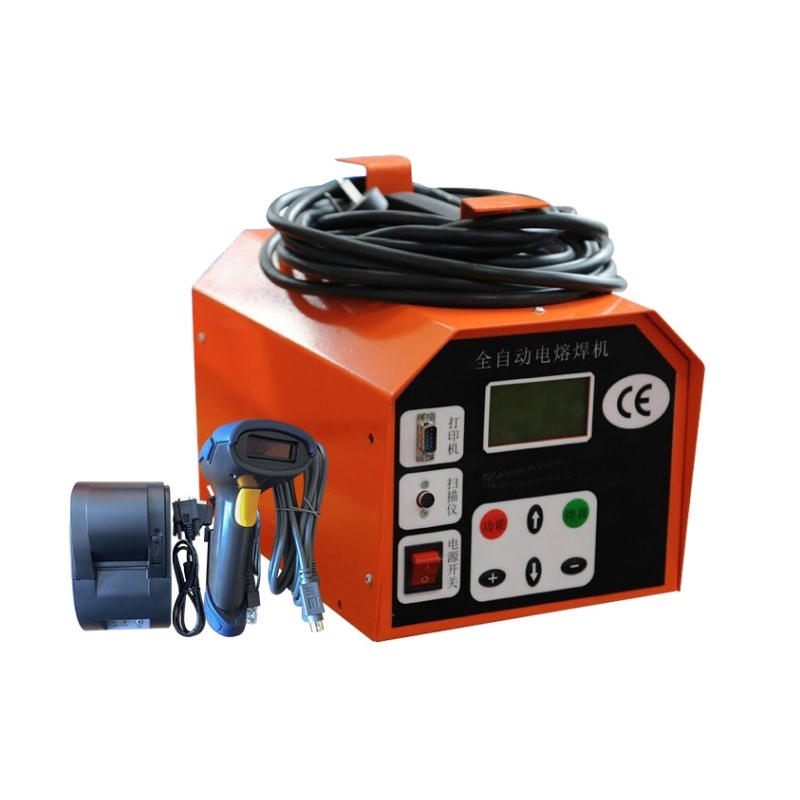
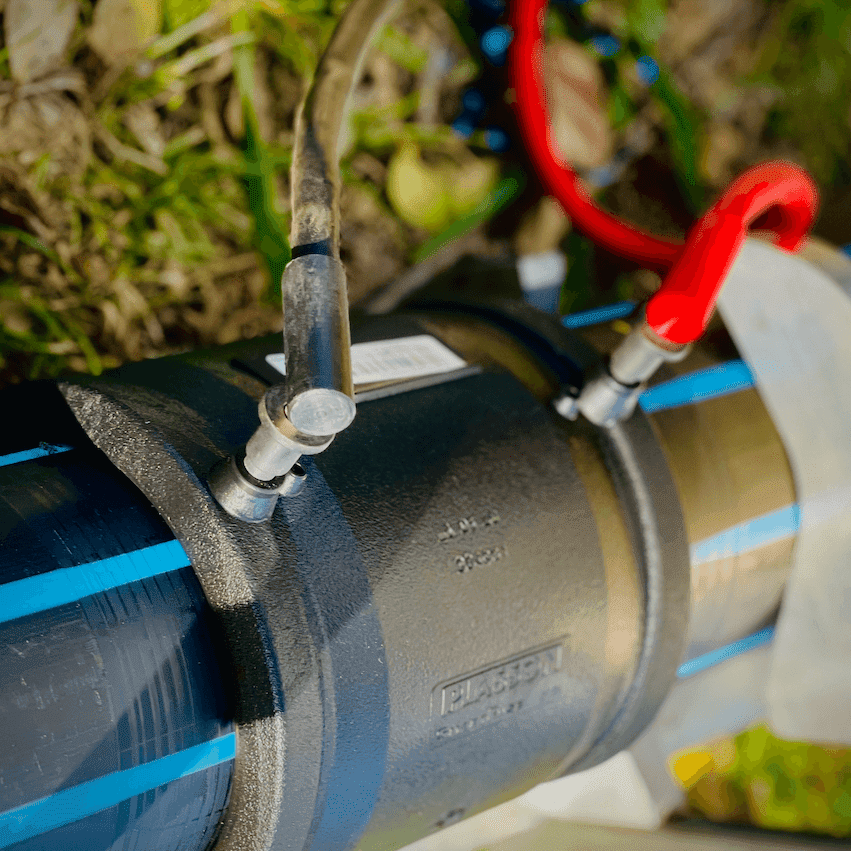
Choosing an HDPE Pipe Welding Machine:
When selecting a welding machine for HDPE pipes, consider the following factors:
- Pipe Size Range: Choose a machine that can handle the diameter of the pipes you plan to work with.
- Type of Welding: Decide whether butt fusion or electrofusion is more suitable for your project.
- Portability: If you need to transport the machine frequently, look for a model that is lightweight and easy to move.
- Power Source: Machines may operate on hydraulic, electric, or pneumatic power.
- Brand & Quality: Choose reputable manufacturers like Rothenberger, Georg Fischer, WIDOS, Fusion Group, or McElroy.
Applications of HDPE Pipe Welding Machines:
- Water Supply: HDPE pipes are commonly used for potable water distribution due to their resistance to corrosion.
- Gas Pipelines: HDPE is also ideal for natural gas distribution networks.
- Sewage & Drainage: HDPE's resistance to chemicals makes it a good choice for wastewater systems.
- Mining & Industrial Use: HDPE pipes are used for slurry transport, cooling systems, and more.
Maintenance and Care:
To ensure long-lasting performance of your welding machine, regular maintenance is key:
- Keep the clamping system and heater plates clean.
- Check the calibration of the pressure and temperature control system.
- Ensure proper storage when not in use to protect the machine from external damage.
Would you like more specific recommendations on models or further details on a particular welding method?
You are welcome to : phone call, Message, Wechat, Email& Seaching us, etc.