Introduction
The Butt Fusion Welding Machine is a hdpe pipe welding equipment of equipment used for connecting thermoplastic materials, such as polyethylene (PE), polypropylene (PP), HDPE, and PVDF pipes and fittings. It operates by heating the ends of two pipes until they melt, then pressing them together under controlled pressure to form a strong, seamless joint.
Main Components
- Heating Plate
Responsible for heating the pipe ends. The heating plate is usually coated with a non-stick material to prevent the pipes from sticking to it. - Clamps
These hold the pipes in place during welding, ensuring proper alignment. The clamps keep the pipes from moving, which is crucial for maintaining weld quality. - Hydraulic Unit
Provides the pressure needed to press the melted pipe ends together. The pressure is adjustable to accommodate different pipe diameters and materials. - Control System
Modern butt fusion welding machines are equipped with electronic control systems that precisely regulate heating time, temperature, and pressure, ensuring consistent and high-quality welds.
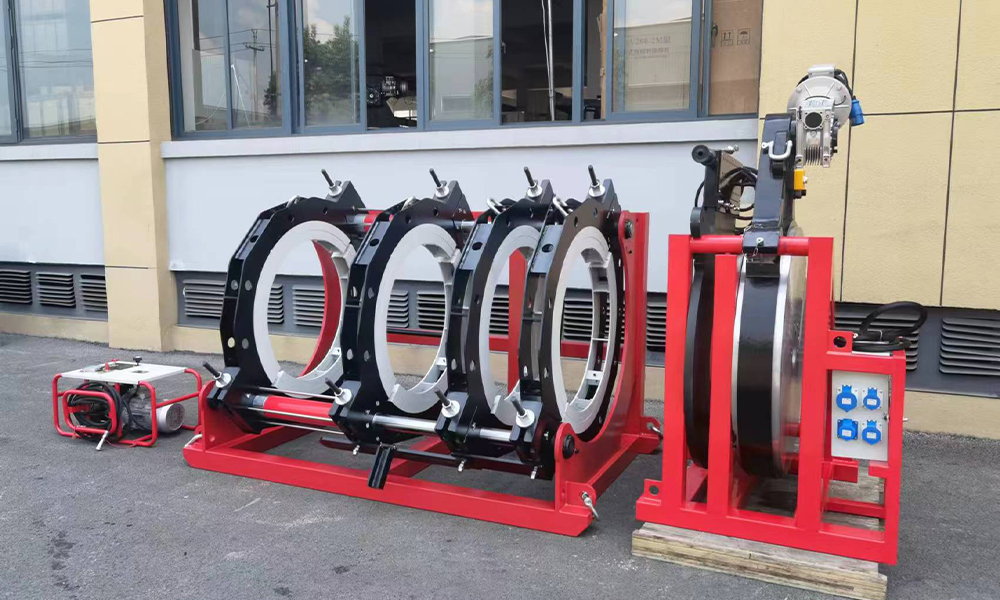
Application Areas
- Water Supply Systems
Used for connecting water supply pipes, especially in urban and rural networks. The resulting joints are strong and seamless, effectively preventing leaks. - Drainage Systems
Widely applied in sewage treatment and stormwater drainage systems. The sealed joints prevent contaminants from leaking, protecting the environment. - Gas Distribution
Utilized in pipelines for natural gas, liquefied petroleum gas (LPG), and other gas distributions, ensuring the joints can withstand high pressure and maintain safety. - Chemical Pipelines
In chemical plants, it is used to transport corrosive liquids, gases, or solid particles. The welding technology ensures that the pipe joints are corrosion-resistant and durable. - Pharmaceutical Industry
Applied in the transport systems for pure water, process water, and wastewater in pharmaceutical plants, where the joints must meet high standards of cleanliness. - Irrigation Systems
Used for connecting various types of plastic pipes in farmland irrigation systems, ensuring stable and efficient water delivery. - Water-Saving Irrigation
In drip and sprinkler irrigation systems, the seal and strength of the welded joints are critical for saving water and improving irrigation efficiency. - Geothermal Heat Pump Systems
Used for connecting pipes in geothermal heat pump systems, ensuring long-term stability of underground pipelines. - Heating Systems
Ensures that welded joints in heating pipelines can withstand long-term thermal expansion and pressure changes, both inside and outside buildings.
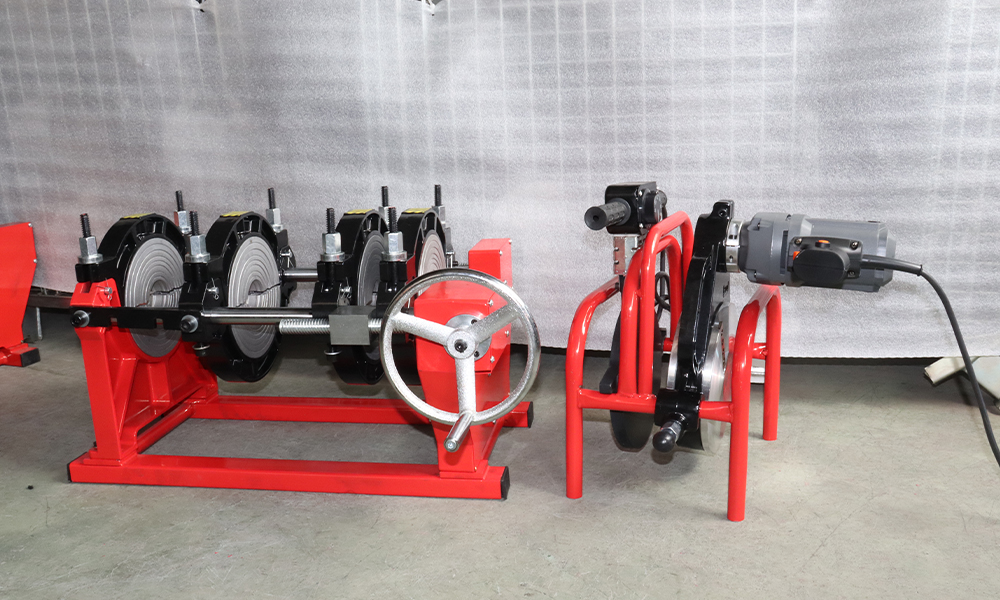
Operational Steps
- Equipment Inspection and Preparation
Before operation, ensure that all machine components (such as the heating plate, clamps, and hydraulic system) are functioning properly. The heating plate should be smooth and scratch-free, and the clamps should be secure. Ensure the work area is clean and level, free from any debris that could affect weld quality. If necessary, set up protective covers to shield the welding process from wind or rain. Clean the pipe ends thoroughly using a specialized cleaner or cloth, removing any dust, oil, or other contaminants. - Clamping and Alignment
Place the pipes into the machine's clamps, ensuring they are evenly distributed on both sides. Adjust the clamps to ensure the pipe ends are perfectly aligned. If the pipe ends are uneven or misaligned, it may affect the uniformity and strength of the weld. Use measurement tools or visual checks to confirm alignment. Adjust as needed before heating. - Facing
Insert the facer between the pipe ends and start the facing process to smooth and even out the pipe ends. Once facing is complete, turn off the facer and remove any shavings from the pipe ends. Check the ends to ensure they meet the required flatness and smoothness. - Heating
Preheat the heating plate to the required temperature (typically between 200°C and 250°C, depending on the pipe material). Insert the heating plate between the pipe ends, ensuring full contact with the pipe surfaces. Heat until the pipe ends are uniformly melted, forming an even bead of molten material. The heating time should be adjusted based on the pipe diameter and thickness. - Welding and Joining
Once the pipe ends have reached the required molten state, quickly remove the heating plate, ensuring the molten surfaces do not become contaminated. Immediately press the pipe ends together under the specified pressure. Maintain even pressure to ensure a high-quality weld. Keep the pressure steady, allowing the pipe ends to bond firmly. A uniform weld bead should form, indicating a successful weld. - Cooling
Maintain pressure until the joint is completely cooled. Cooling time depends on the pipe diameter and ambient temperature. Once cooled, release the clamps and remove the pipe. Inspect the weld bead to ensure there are no cracks, voids, or other defects. - Post-Weld Treatment
Conduct a visual inspection or use specialized testing equipment to check the weld quality, ensuring it meets required standards. Record all welding parameters (such as heating time, temperature, and pressure) for future reference or quality traceability.
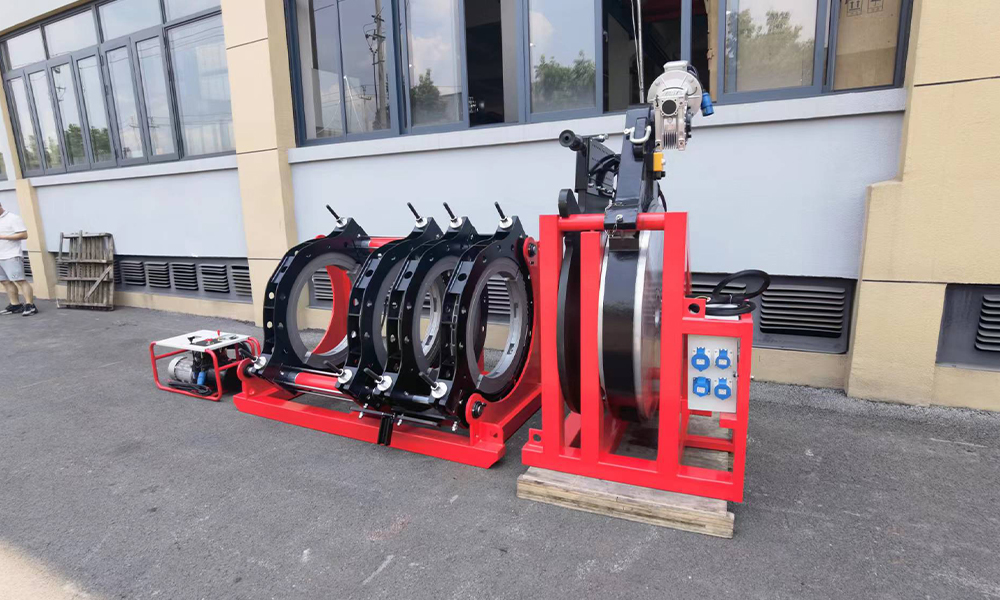
Precautions
- Pipe Cleaning
Before welding, thoroughly clean the pipe ends to remove dust, dirt, grease, and other contaminants. These impurities can affect the weld quality, leading to weak or improperly sealed joints. - Temperature Control
The heating plate temperature must be strictly controlled, typically between 200°C and 250°C, depending on the material. If the temperature is too low, the pipe may not melt sufficiently; if too high, the pipe may over-melt or deform, compromising the weld. - Pressure Control
Adjust the welding pressure based on the pipe diameter and material properties. Excessive pressure may cause excessive melt, forming "weld flash"; insufficient pressure may prevent the pipe ends from fusing properly, weakening the joint. - Cooling Time
After welding, maintain pressure until the weld joint is fully cooled and solidified. Releasing the pressure too early can cause deformation or cracks at the joint, affecting the weld quality. - Equipment Maintenance
Regularly inspect and maintain the Butt Fusion Welding Machine, paying special attention to the heating plate's surface and the hydraulic system for any signs of wear or leaks. Proper equipment maintenance is crucial for ensuring consistent weld quality. - Operating Standards
Operators should be professionally trained and familiar with the equipment's operation and safety requirements. Follow the operating procedures strictly to avoid accidents or welding failures due to improper handling. - Environmental Requirements
Ensure that the welding process is protected from wind, sand, or rain, which can contaminate the weld surface or affect temperature control. If necessary, set up temporary shelters to ensure a controlled welding environment.
By following these steps and precautions, the Butt Fusion Welding Machine can consistently produce high-quality welds, ensuring the durability and longevity of the pipeline system.
You are welcome to : phone call, Message, Wechat, Email& Seaching us, etc.